What is a Hydraulic Press Brake?
A hydraulic press brake is a machine used in the metalworking industry to bend and shape sheet metal. It utilizes hydraulic force to apply pressure on a metal sheet, resulting in precise bends and shapes. The machine consists of several components, including a hydraulic cylinder, a ram, a table, and a die.
The hydraulic press brake works by using hydraulic pressure to move the ram (a large, flat plate) downward towards the table and the die. The die, which is mounted on the table, applies pressure on the metal sheet, causing it to bend or shape according to the desired specifications.
The hydraulic system provides the force necessary to bend the metal, and it is controlled by an operator using a control panel or computer numerical control (CNC) system. The operator can adjust various parameters such as the bending angle, speed, and back gauge position to achieve the desired results.
Hydraulic press brakes offer several advantages over other types of bending machines. Firstly, they provide precise and accurate bending, ensuring high-quality and consistent results. The hydraulic system allows for excellent control over the bending process, resulting in less material waste. Additionally, hydraulic press brakes are versatile and can handle a wide range of materials and thicknesses. They can be used to create simple bends or complex shapes, making them suitable for various applications in industries such as manufacturing, construction, metal fabrication, and more.
In summary, a hydraulic press brake is a machine that utilizes hydraulic force to bend and shape sheet metal. It offers precise bending capabilities, versatility, and control over the bending process, making it an essential tool in the metalworking industry.
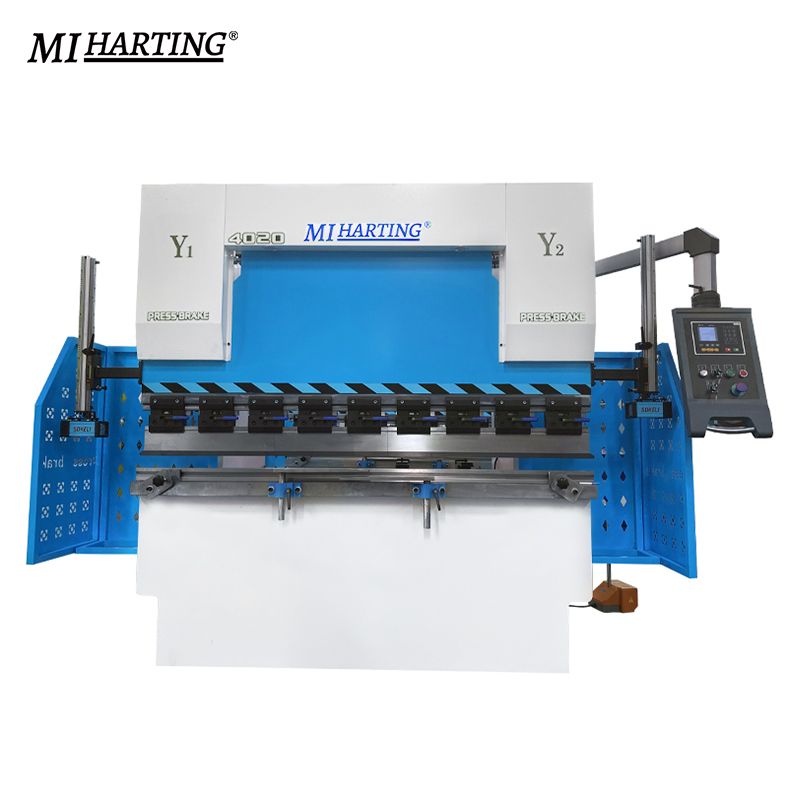
How Does a Hydraulic Press Brake Differ from Other Press Brakes?
- 1. Power Source: Hydraulic press brakes use hydraulic power to generate force, while mechanical press brakes rely on mechanical mechanisms like flywheels and linkages. Pneumatic press brakes, on the other hand, use compressed air or gas to generate force.
- 2. Force Generation: Hydraulic press brakes use hydraulic cylinders to apply force on the metal sheet, allowing for precise control and adjustment of the bending process. Mechanical press brakes use a mechanical system, typically a motor and a mechanical linkage, to generate force. Pneumatic press brakes use air pressure to create force.
- 3. Bending Capacity: Hydraulic press brakes are known for their high bending capacity. They can handle thick and heavy-duty materials with ease, making them suitable for industrial-scale production and heavy metalworking applications. Mechanical press brakes have limited bending capacities compared to hydraulic ones. Pneumatic press brakes are typically used for lighter gauge materials and smaller-scale operations.
- 4. Control and Precision: Hydraulic press brakes offer superior control and precision over the bending process. The hydraulic system allows for fine adjustments of parameters such as bending angle, speed, and back gauge position. This level of control ensures consistent and accurate bending results. Mechanical press brakes offer less control and may require manual adjustments. Pneumatic press brakes also provide good control but are generally not as precise as hydraulic ones.
- 5. Flexibility: Hydraulic press brakes are highly versatile and can handle a wide range of materials and thicknesses. They can be used for simple bends as well as complex shapes. Mechanical press brakes may have limitations in terms of material thickness and shape complexity. Pneumatic press brakes are suitable for lighter gauge materials and simpler bending requirements.
What are the Key Components of a Hydraulic Press Brake?
Hydraulic System: The hydraulic system is the heart of a hydraulic press brake. It consists of a hydraulic pump, hydraulic cylinders, valves, and hoses. The hydraulic pump generates pressure to drive the hydraulic cylinders, which apply force to the bending tool.
Bending Tool: The bending tool, also known as the punch and die, is responsible for deforming the metal sheet during the bending process. It is typically made of hardened steel and comes in various shapes and sizes depending on the desired bend.
Back Gauge: The back gauge is a mechanism that supports and positions the metal sheet accurately during bending. It ensures consistent and repeatable bending results. The back gauge can be manually adjusted or controlled by a motorized system.
Control System: The control system of a hydraulic press brake allows operators to set and adjust various parameters such as bending angle, speed, and back gauge position. It may include a control panel with buttons, switches, and a display screen for monitoring and programming the bending process.
Frame and Bed: The frame provides the structural support for the hydraulic press brake, while the bed provides a flat surface on which the metal sheet rests during bending. The frame and bed are usually made of heavy-duty steel to withstand the forces involved in the bending process.
Safety Features: Hydraulic press brakes are equipped with various safety features to protect operators and prevent accidents. These may include safety light curtains, emergency stop buttons, two-hand controls, and safety interlocks.
Hydraulic Fluid and Reservoir: Hydraulic press brakes require hydraulic fluid to transfer power and operate the hydraulic system. The hydraulic fluid is stored in a reservoir and circulated through the system to maintain proper lubrication and cooling.
Control Pedals: Control pedals, such as foot pedals, are used to activate the hydraulic system and control the movement of the bending tool. They allow operators to initiate the bending process and control the speed and pressure applied during bending.
What are the Advantages of a Hydraulic Press Brake?
- 1. High Bending Capacity: Hydraulic press brakes have a high bending capacity, making them ideal for heavy-duty and industrial-scale metalworking applications. They can handle thick and heavy materials with ease.
- 2. Precise Control: Hydraulic press brakes offer precise control over the bending process, allowing for consistent and accurate results. The hydraulic system allows for fine adjustments of parameters such as bending angle, speed, and back gauge position.
- 3. Versatility: Hydraulic press brakes are highly versatile and can handle a wide range of materials and thicknesses. They can be used for simple bends as well as complex shapes, making them suitable for various metalworking applications.
- 4. Energy Efficiency: Hydraulic press brakes are energy-efficient compared to mechanical press brakes since they only use power when needed. The hydraulic system can also recycle energy, reducing overall energy consumption.
- 5. Reduced Maintenance: Hydraulic press brakes require less maintenance compared to mechanical press brakes since they have fewer moving parts. The hydraulic cylinders and pumps are sealed units that require minimal maintenance.
- 6. Safety: Hydraulic press brakes come equipped with various safety features, such as safety light curtains, emergency stop buttons, two-hand controls, and safety interlocks, to protect operators and prevent accidents.
How to Maintain a Hydraulic Press Brake?
- 1. Regular Inspection: Inspect the hydraulic press brake regularly for any signs of wear and tear, damage, or leaks in the hydraulic system, hoses, and components.
- 2. Routine Cleaning: Keep the machine clean and free from debris or foreign matter that can cause damage to the hydraulic system or components. Use a soft cloth and mild cleaning solution to wipe the machine down after each use.
- 3. Lubrication: Lubricate the hydraulic system and components regularly to prevent friction and wear. Use high-quality lubricants recommended by the manufacturer.
- 4. Filter Replacement: Replace the hydraulic fluid filter regularly to maintain proper fluid flow and prevent contamination.
- 5. Hydraulic Fluid Level: Check the hydraulic fluid level regularly and top up as needed. Use only the recommended type of hydraulic fluid.
- 6. Cylinder Maintenance: Check the hydraulic cylinders regularly for any signs of damage or leaks. Replace any damaged cylinders or seals promptly.
- 7. Back Gauge Calibration: Calibrate the back gauge periodically to ensure accurate positioning of the metal sheet during bending.
- 8. Control System Inspection: Inspect the control system, including the control panel, buttons, switches, and display screen, regularly for any signs of damage, wear, or malfunction.
- 9. Safety Features: Check the safety features regularly to ensure they are functioning correctly. Repair or replace any damaged or malfunctioning safety features promptly.
- 10. Professional Inspection: Have a qualified technician inspect the hydraulic press brake periodically to identify any potential issues and perform any necessary repairs or maintenance.
By following these maintenance tips, you can keep your hydraulic press brake in excellent condition and ensure optimal performance and safety.
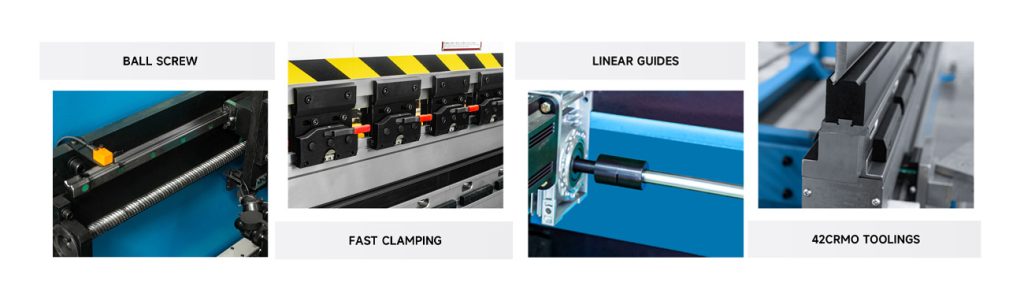