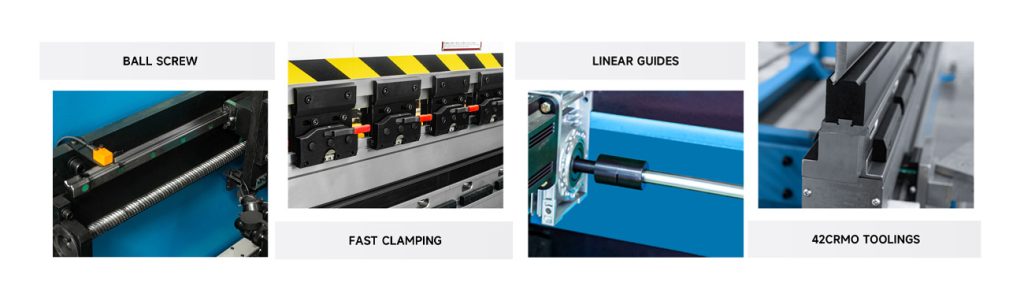
Sheet metal bending is a fundamental process in the field of metal fabrication that involves shaping flat metal sheets into desired forms and structures. This essay aims to delve into the different types of sheet metal bending techniques, discussing their characteristics, applications, and advantages.
V-Bending:
V-bending is a widely used technique in which a sheet metal is bent between a punch and a die with a V-shaped groove. This method enables precise control over bending angles and is commonly employed in industries such as automotive, aerospace, and electronics.
U-Bending:
Similar to V-bending, U-bending results in a U-shaped bend. It is often utilized to create channels, rounded edges, or components with curved profiles. U-bending finds applications in HVAC systems, furniture manufacturing, and architectural projects.
Air Bending:
Air bending is a versatile technique that involves bending the sheet metal using a punch and die without touching the bottom of the die. The angle of the bend is determined by the depth to which the punch penetrates the die. Air bending offers flexibility in terms of bend angles and is suitable for various materials and thicknesses.
Bottoming:
Bottoming, also known as coining, involves bending the sheet metal to the bottom of the die to achieve a sharp bend with minimal spring back . This technique is commonly used for precision bending, where accuracy and repeatability are crucial. Bottoming is often employed in the production of electrical enclosures, medical equipment, and intricate components.
Folding:
Folding is a technique that allows sheet metal to be bent along a straight line without the use of a punch and die. It is commonly used for creating flanges, boxes, or simple bends. Folding provides a quick and cost-effective solution for bending applications such as sheet metal enclosures, cabinets, and brackets.
Rotary Bending:
In rotary bending, the sheet metal is bent around a rotating die. This technique is suitable for creating cylindrical or curved shapes, such as tubes, pipes, and rounded profiles. Rotary bending is commonly used in industries like automotive, construction, and manufacturing.
Roll Bending:
Roll bending involves passing the sheet metal through a series of rollers to achieve a curved or cylindrical shape. This method is commonly used for large-scale bending applications, such as the production of pipes, tubes, and structural components. Roll bending offers high efficiency and accuracy for achieving consistent bends.
Incremental Bending:
Incremental bending involves bending the sheet metal in small increments to achieve complex shapes or curves. This technique is often used in the automotive and aerospace industries, where intricate designs and precise tolerances are required. Incremental bending allows for greater flexibility and control over the bending process.
Conclusion:
Sheet metal bending encompasses a range of techniques, each with its own advantages and applications. The choice of bending technique depends on factors such as the desired shape, material thickness, complexity of the design, and production requirements. Understanding the different types of sheet metal bending techniques is essential for manufacturers and fabricators to select the most appropriate method for their specific needs, ensuring efficient and accurate production processes.
What is a hydraulic press brake ?
The working principle of the hydraulic bending machine is to use the pressure generated by the hydraulic cylinder and the hydraulic system to clamp the upper mold and the lower mold to the metal sheet, and then apply force to make it bend. The hydraulic system consists of hydraulic pumps, hydraulic cylinders, control valves and fuel tanks. The operator controls the work of the hydraulic system through the buttons on the control panel or the pedals.
The main components of the hydraulic bending machine include the frame, the upper mold, the lower mold, the hydraulic cylinder, the hydraulic pump, the control system and the safety device, etc. The frame is the structural frame that supports and fixes the components, and the upper and lower dies are used to clamp and bend the sheet metal. Hydraulic cylinders are key components for generating and transmitting pressure, and hydraulic pumps provide hydraulic energy. The control system is used to control the work of the hydraulic system to ensure accurate ben ding operation. Safety devices include light curtains, safety doors, emergency stop buttons, etc., to ensure the safety of operators.
The tonnage capacity of a hydraulic bending machine refers to the maximum pressure capacity it can generate, usually in tons. The larger the tonnage capacity, the greater the material thickness and bending angle that the hydraulic press brake can handle.
In short, the hydraulic bending machine is an important equipment widely used in sheet metal processing. It has the characteristics of high strength, high precision and high efficiency, and can meet various sheet metal processing needs.
Advantages of hydraulic press brakes
1.The whole EU streamlined design, heat treatment rack, high rigidity worktable, optional mechanical compensation device, to achieve precision bending.
2.Hydraulic synchronous control and NC or CNC programmable logic controller ensure accurate repeatability and ease use.
3. Integrated hydraulic system (Bosch Rexroth Germany) allows automatically switch to slow bends in a quick way.
4. X axis , Y axis , Z axis ,R axis and V axis realize accurate positioning function by frequency converter through NC or CNC system programming control.
5.Cutting-edge frequency response hydraulic control technology, more stable machine tools, more reliable operation.
6.The best ratio of parameters, optimal core configuration ensure stable performance, more convenient operation.
Safety considerations for the press brake operator
1.Training and operating procedures: Operators should receive thorough training before operating a hydraulic press brake. They should be familiar with the machine's operating procedures and safety protocols. They should know the various components and control systems of the machine and how to operate and adjust it correctly.
2.Safety devices: Hydraulic press brakes are typically equipped with multiple safety devices, such as light curtains, safety gates, emergency stop buttons, etc. These devices monitor and detect the safety of the operating area and immediately stop the machine in case of any hazardous situations, ensuring the safety of the operator.
3.Personal protective equipment (PPE): Operators should wear appropriate PPE when operating a hydraulic press brake, including safety glasses, earplugs, gloves, and protective clothing. These equipment protect them from potential hazards such as flying metal fragments, noise, and chemicals.
4.Safe operation: Operators should follow the operating procedures and safety protocols when operating a hydraulic press brake. They should adhere to the correct working steps, ensure proper clamping and positioning of the metal sheet, and avoid placing fingers or other body parts in the danger zone.
5.Regular maintenance and inspection: Hydraulic press brakes require regular maintenance and inspection to ensure their proper functioning and safety. This includes lubrication system maintenance, bolt checks, calibration of sensors and safety devices, etc. Regular maintenance helps reduce machine failures and the occurrence of accidents.