Hydraulic bending machines play a crucial role in various industries that involve metal fabrication. These machines utilize hydraulic power to bend metal sheets, providing accuracy and efficiency in the manufacturing process. In this article, we will explore the application of hydraulic bending machines and discuss the importance of regular maintenance for their optimal performance.
Applications of Hydraulic Bending Machines
Hydraulic bending machines are widely used in industries such as automotive, aerospace, construction, and metalworking. They are primarily employed to bend metal sheets into desired shapes and angles for various components, including brackets, frames, panels, and more. The versatility of hydraulic bending machines makes them indispensable in these industries.
Working Principle of Hydraulic Bending Machines
Hydraulic bending machines function based on the principle of hydraulic power transmission. The machine consists of a hydraulic system, a bending die, and a pressure die. When hydraulic pressure is applied, the bending die exerts force on the metal sheet, causing it to bend at the desired angle. The pressure die ensures precise bending by holding the sheet firmly in place during the process.
Importance of Regular Maintenance
Regular maintenance is essential to ensure the optimal performance and longevity of hydraulic bending machines. Proper maintenance helps prevent breakdowns, reduces downtime, and extends the lifespan of the machine. Neglecting maintenance can result in decreased efficiency, inaccurate bending, and potential safety hazards.
Daily Maintenance Routine
To maintain a hydraulic bending machine, a daily maintenance routine should be followed. This routine includes:
a) Cleaning: Regularly clean the machine to remove debris, dust, and metal shavings. Pay attention to the bending die and pressure die areas, as they are prone to buildup.
b) Lubrication: Apply lubrication to all moving parts, such as the hydraulic cylinder, guides, and pivot points. This helps reduce friction and ensures smooth operation.
c) Inspection: Perform a visual inspection to check for any signs of wear, damage, or loose components. Pay attention to the hydraulic hoses, seals, and fittings for any leaks or abnormalities.
d) Calibration: Periodically check and calibrate the machine to ensure accurate bending angles. Use precision measuring tools to verify the alignment of the bending die and pressure die.
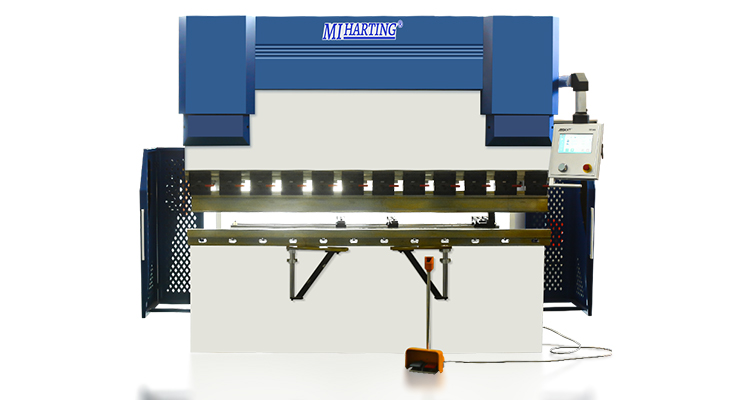
3200 Hydraulic Press Brake with TP10S Controller Sheet Metal Bending Machine
Preventive Maintenance Measures
In addition to daily maintenance, preventive maintenance measures should be implemented to avoid major breakdowns and costly repairs. These measures may include:
a) Regular Servicing: Schedule routine servicing by a qualified technician to inspect and maintain critical components of the hydraulic system, such as the pump, valves, and filters.
b) Replacement of Wear Parts: Identify and replace worn-out parts, such as seals, gaskets, and hoses, to prevent hydraulic leaks and maintain optimal performance.
c) Training and Operator Awareness: Provide training to operators on proper machine operation and maintenance procedures. Encourage operators to report any abnormalities or issues promptly.
Safety Considerations
Safety is paramount when working with hydraulic bending machines. Operators should receive proper training on machine operation, safety protocols, and emergency procedures. Personal protective equipment, such as gloves and safety glasses, should be worn at all times. Regularly inspect safety features of the machine, including emergency stop buttons and safety guards.
Conclusion
Hydraulic bending machines are versatile tools used in various industries for precision sheet metal bending machine. Daily maintenance routines, preventive measures, and adherence to safety protocols are vital for their efficient operation and longevity. By investing time and effort into regular maintenance, businesses can ensure optimal performance and maximize the lifespan of their hydraulic bending machines.