Beveling edges on metal plates or sheet metal is a common and important process in the metalworking industry. It involves creating an angled or chamfered edge on the material, which can serve various purposes such as improving aesthetics, enhancing weldability, or facilitating assembly. One efficient and precise method for beveling edges is by using a laser cutting machine.
To prepare the material edge for welding, fabricators often employ bevel cuts on sheet metal. Beveled edges increase the surface area for welding, facilitating better material penetration on thick parts and resulting in stronger and more stress-resistant welds. Achieving precise and uniform bevel cuts with the appropriate inclination angles is crucial for producing weldments that meet the required codes and tolerance specifications. Inconsistencies in the bevel cuts throughout their length can hinder automated welding from achieving the desired quality, necessitating manual welding to ensure better control over the flow of filler metal.
Laser technology offers a solution for beveling in metal fabrication, aiming to minimize costs and streamline operations. Laser cutting machines equipped with 3D heads and five interpolated axes can perform various processes, including hole drilling, beveling, and marking, in a single cycle without the need for additional post-processing steps. These lasers can precisely execute interior bevels throughout the length of the cut and create high-tolerance, straight, and tapered small-diameter holes.
The 3D bevel head in laser cutting machines provides rotation and tilt capabilities of up to 45 degrees, enabling the cutting of different bevel shapes, such as internal contours, variable bevels, and multiple bevel contours (Y, X, or K). It allows direct beveling of materials ranging from 1.37 to 1.57 inches thick, depending on the application and bevel angles, and offers a cut angle range of -45 to +45 degrees.
The X bevel, commonly used in shipbuilding, railway component manufacturing, and defense applications, is essential when welding can only be performed from one side. With angles typically ranging from 20 to 45 degrees, the X bevel is frequently employed for welding sheets up to 1.47 inches thick.
Tests conducted on 0.5-inch-thick grade S275 steel plates with SG70 welding wire demonstrated the advantages of laser cutting for beveling. Laser cutting produced a top bevel with a 30-degree bevel angle and a 0.5-inch high land in the straight cut, resulting in a smaller heat-affected zone compared to other cutting processes. This reduction in the heat-affected zone contributed to improved welding outcomes.
For a 45-degree bevel, the maximum sheet thickness to achieve a total length of 1.6 inches on the bevel surface is 1.1 inches.
The quality of the cut is influenced by the surface roughness, which determines the final finish. Laser cutting machines with 3D heads and interpolated axes are designed to cut complex contours in thick materials with multiple bevel cuts. Minimizing roughness is crucial as it not only affects the appearance of the edge but also the friction properties.
To begin the beveling process using a laser cutting machine, it is essential to have a machine equipped with the necessary features for beveling, such as a tilting head or a rotary axis. These features allow the laser beam to be directed at an angle to the material, creating the desired beveled edge. The machine should also have a robust and accurate control system that allows for precise programming and movement control.
The first step in beveling is to prepare the metal plate or sheet metal for the process. This involves cleaning the surface thoroughly to remove any dirt, oil, or rust that may interfere with the laser cutting process. The material should be securely fixed in place on the laser cutting machine's worktable to prevent any movement during the cutting process. It is important to ensure that the material is properly aligned and positioned to achieve accurate and consistent bevels.
Next, the operator needs to program the laser cutting machine with the appropriate parameters for beveling. This includes setting the desired bevel angle, bevel width, and cutting speed. The specific parameters will depend on the material type, thickness, and the desired bevel specifications. The operator should have a good understanding of the machine's programming interface and follow the instructions provided by the manufacturer.
Once the laser cutting machine is programmed, the operator can initiate the beveling process. The laser beam is directed onto the material, following the programmed path to create the beveled edge. The tilting head or rotary axis of the machine allows the beam to move at an angle, gradually cutting away the material to form the bevel. The machine's control system ensures precise movement and accurate cutting.
During the cutting process, it is crucial to ensure proper ventilation and fume extraction to remove any fumes or particles generated by the laser cutting. This helps maintain a safe working environment and prevents any potential health hazards. The operator should also wear appropriate personal protective equipment (PPE) such as safety glasses and gloves to protect against any potential hazards.
After the beveling process is complete, the operator should inspect the beveled edge for quality and accuracy. Any imperfections or irregularities should be addressed promptly to ensure the desired bevel specifications are met. The operator can use measuring tools such as calipers or micrometers to verify the bevel angle and width. Depending on the application requirements, additional finishing processes such as grinding or sanding may be necessary to achieve the desired surface finish.
In conclusion, beveling edges on metal plates or sheet metal using a laser cutting machine is an efficient and precise method. It allows for the creation of beveled edges with various angles and widths, enhancing the functionality and aesthetics of the metalwork. However, it is important to ensure proper machine setup, programming, and safety measures to achieve high-quality beveled edges. Regular maintenance and calibration of the machine are also crucial to ensure consistent and accurate beveling results. By utilizing laser cutting technology for beveling, fabricators can streamline operations, improve efficiency, and reduce costs in metal fabrication processes. Embrace the power of fiber laser cutting technology and choose the best fiber laser cutting machine for your metal fabrication needs.
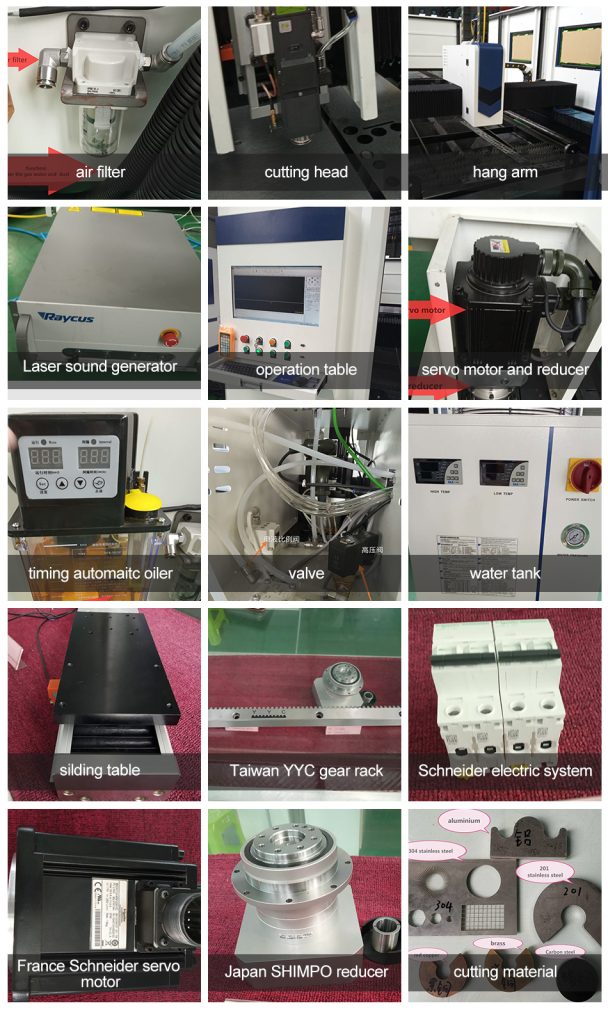